Article
Resources
Article
3D Printing and Modular Construction - A New and Growing Avenue for the Construction Industry
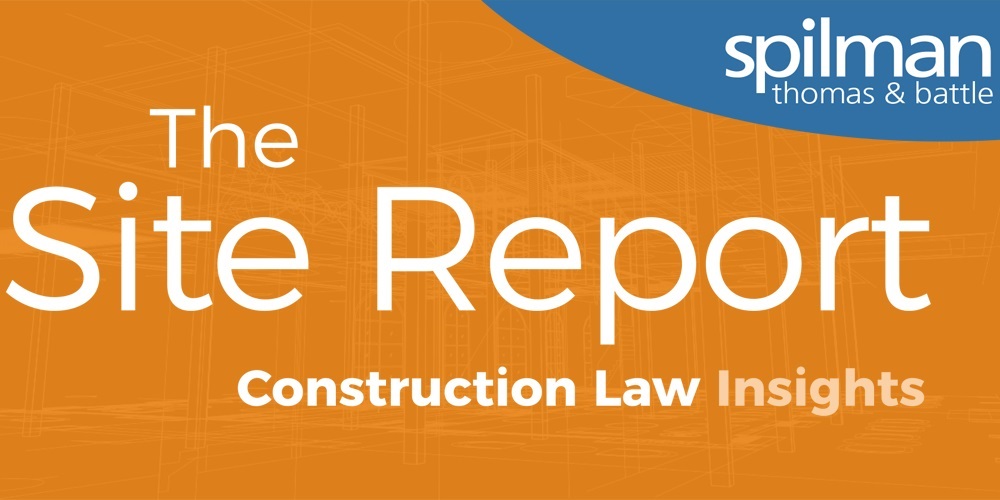
Just as many national, local and company-specific clean energy and sustainability goals are aiming for carbon reduction or carbon neutrality by certain future dates, such as the U.S. federal government’s target of at least 50 percent carbon reduction by 2030, the demand for electricity continues to grow. In fact, the construction industry’s use of electricity is predicted to grow 20 percent by 2030. How can contractors, designers, engineers, architects and building owners help reduce the industry’s carbon emissions and electricity demand at the same time?
One way continues to be evaluating projects for which 3D printing and modular construction are appropriate. We have reported to you many times on the benefits that the innovation of 3D printed homes and buildings bring to the industry: reduced labor intensity, build time reduction, cost savings over traditional “stick built” construction, and lower overall greenhouse gas emissions (Issue 6, 2023; Issue 5, 2023; Issue 3, 2023; Issue 12, 2022 Issue 9, 2022; Issue 5, 2022; Issue 4, 2022; and Issue 2, 2022). As this article highlights, the benefits of 3D printing technology extend beyond on-site construction of the single 3D printed building with regard to the off-site manufacturing of building components. 3D printing also allows for the incorporation of unique shapes to create complex designs more easily. Where challenges such as size limitations, regulatory requirements, and planning to ensure expected performance of electrical, water, heating and other components of the building can be overcome, 3D printing should be evaluated. (Image by ICON)
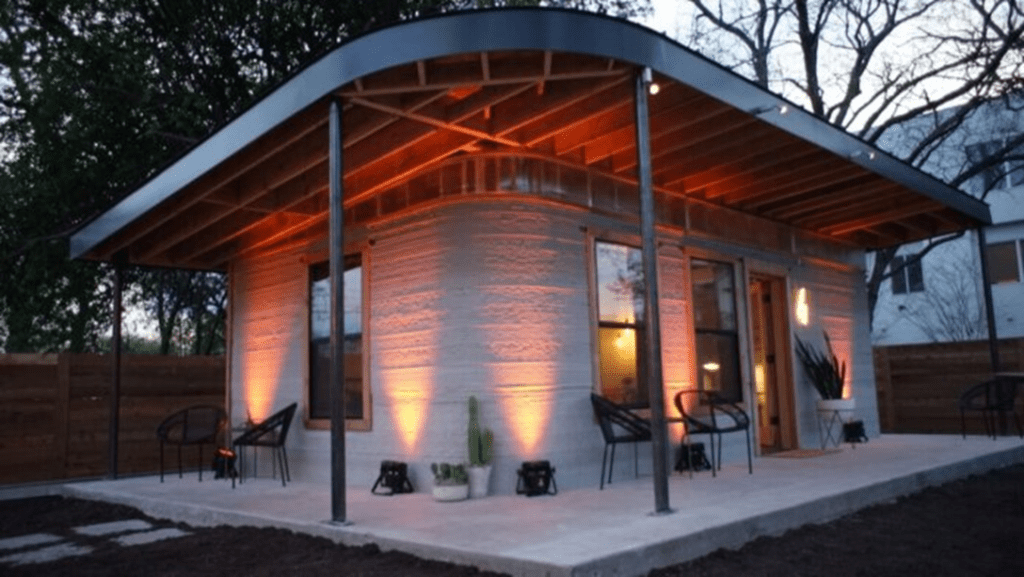
This article also touches upon other technologies that can help reduce carbon emissions and/or electric demands in the construction industry, in part because of time efficiencies these technologies can provide: robots drones and modular wiring systems.
First, the use of robots in construction is expected to grow. Robots are used for welding, surveying, mapping, bricklaying or other repetitive work, and investigating areas on a site that may be unsafe for construction workers to evaluate. The ability of robots to investigate potentially dangerous conditions is especially relevant for project sites and/or existing buildings that have been damaged in extreme weather events. One of the construction industry robots is Hilti’s semi-autonomous robot called Jaibot which uses BIM data to locate and drill holes for electrical and plumbing lines. (Image by Hilti)
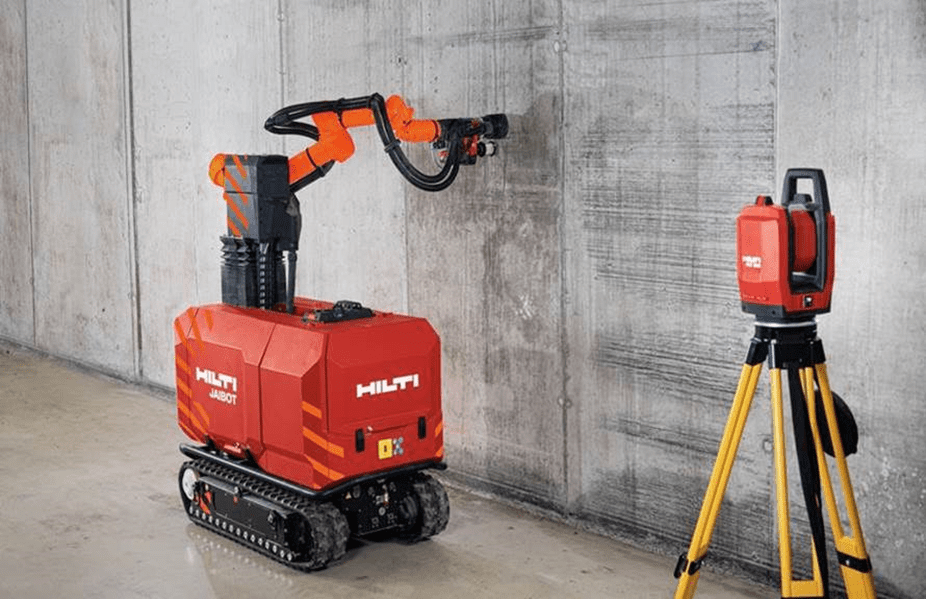
Second, the article briefly touches on the advantages of using drones on construction projects. As we have informed you in prior editions of The Site Report (Issue 8, 2024; Issue 8, 2023; Issue 1, 2023; Issue 12, 2022; Issue 9, 2022; Issue 6, 2022; and Issue 1, 2022); drones have been used to improve construction projects when used as “digital construction assistants,” where drones are able to document site conditions and work progress on a real-time basis, in an efficient manner, and offer an aerial view of larger projects. The advantages of using drones over using construction workers for surveying a site, for example, are improved efficiency and data accuracy and reduced expenses. This is because traditional manual surveying can take a skilled surveying team an hour to survey approximately five acres. Compare this to beginner surveyors using drones to survey 120 acres per hour, which equates to a substantial reduction in cost and time to complete a construction project. Drones can also be used to survey dangerous conditions, such as worksite accidents, fires, and challenging terrain, which alleviates danger to the workforce. (Image from propeller)
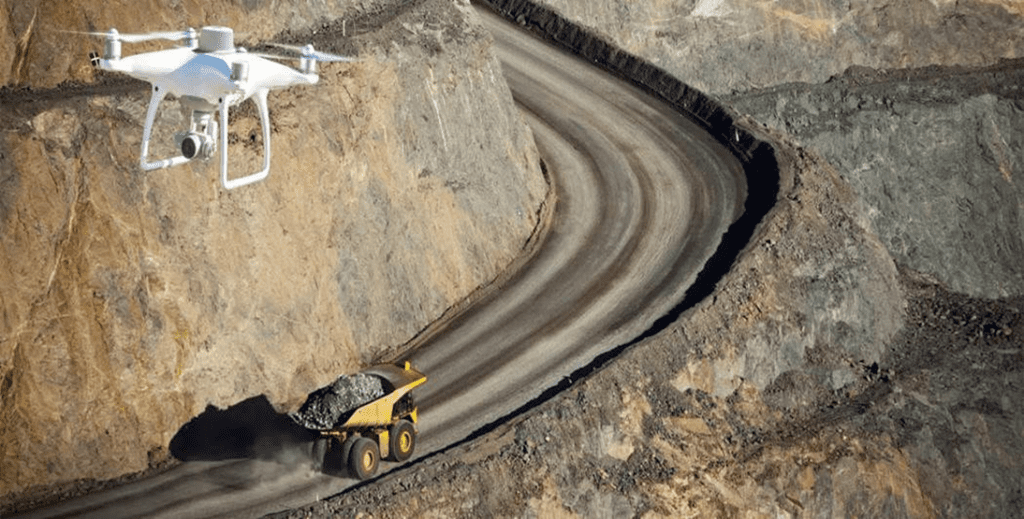
Third, the article describes how the use of modular wiring systems (MWS) can provide safe and efficient solutions used in hospitals, schools, government and other buildings. MWS are pre-assembled wiring assemblies that replace traditional branch circuit wiring and components. MWS is cost-effective, flexible, and user-friendly as compared to traditional electrical installation, with an estimated reduction in the time to install electrical systems by up to 75 percent, which in turn reduces overall construction time and electric demand for the project. (Image from Panel Built, Inc.)

In all, these technologies will make a positive change for the environment, will reduce construction time, costs and electric usage, and will improve worker safety for the entire construction industry.